PATIG :Manufacturer of Spark plug wire and horn
about us:
Part Tis Gyan Company with Patig brand By creating management systems was able to obtain ISO 9001 quality management certificates, IATF 16949 automotive standard and ISO / IEC 17025 laboratory standard. For the needs of the automotive industry and the auto spare parts market, products offers with high quality, reasonable prices and timely delivery.
our customers :
Saipaydak, Isako, Megamotor, Dina Part, Ezam
Company Profile | |
Company Name |
Part Tis Gian |
Brand |
Patig |
Tel |
08133429522 |
Managing Director |
Mahdi Molavi |
Mobile |
09127980286 |
Fax |
08133429523 |
Address |
No:136 Street:5 , Industrial Town Nahavand,Hamedan. IRAN |
Postal code |
6597168996 |
No. of employees |
28 |
Established Year |
2011 |
Field of Business |
Manufacturer of Auto Parts |
Main product |
Spark plug wire and horn |
Total Site Area |
2000 m2 |
production capacity |
400000 set |
Molavi.md@gmail.com |
Description:
High tension leads or high tension cables or spark plug wires or spark plug cables or Ignition Wire Set are the wires that connect a distributor, ignition coil, or magneto to each of the spark plugs in some types of internal combustion engine. "High tension lead" or "cable" is also used for any electrical cable carrying a high voltage in any context. Tension in this instance is a synonym for voltage. High tension leads, like many engine components, wear out over time. Each lead contains only one wire, as the current does not return through the same lead, but through the earthed/grounded engine which is connected to the opposite battery terminal (negative terminal on modern engines) high tension may also be referred to as HT.
Spark plug wires have an outer insulation several times thicker than the conductor, made of a very flexible and heat-resistant material such as silicone or EPDM rubber. The thick insulation prevents arcing from the cable to an earthed engine component. A rubber "boot" covers each terminal. Dielectric grease can be used to improve insulation; a small amount can be applied in the inside of the rubber boot at each end of each wire to help seal out moisture. Printing on spark plug wires may include a brand name, insulation thickness (in millimeters), insulation material type, cylinder number, and conductor type (suppressor or solid wire).
The wire from each spark plug is just long enough to reach the distributor, without excess. Each end of a spark plug wire has a metal terminal that clips onto the spark plug and distributor, coil, or magneto. There are dedicated spark plug wire pliers, tools designed for removing the terminal from a spark plug without damaging it.
To reduce radio frequency interference (RFI) produced by the spark being radiated by the wires, which may cause malfunction of sensitive electronic systems in modern vehicles or interfere with the car radio, various means in the spark plug and associated lead have been used over time to reduce the nuisance:
1.Copper conductors (no suppression)
2.Resistor in spark plug with copper conductor
3.Compressed carbon powder as conductor in the lead to act as a resistor
4.Stainless steel wire wound as a coil in the lead with a resistance of about 1300 ohms/meter since 1980s. This acts as an inductor and a resistor
During the production of the spark plug cable, the presence of residual dielectric is often found. This deposit affects the conductivity characteristics of the wire, creating a more or less important resistance that does not allow the wire to pass the routine tests. The patent of the company Brecav[1] allowed to pursue the improvement of the quality standards of production of the spark plug wire and a certification of the working hours of the spark plug cable.
Placing spark plug wires back into their separators or holders during replacement helps to keep them in place despite engine vibration, extending their life. A common problem with spark plug wires is corrosion of the metal end terminals. Better-quality spark plug wires usually have brass terminals, which are more resistant to corrosion than other metals used.
Older engines also have a wire connecting the ignition coil to the distributor, known as a coil wire. A coil wire is of the same construction as a spark plug wire, but generally shorter and with different terminals. Some distributors have an ignition coil built inside them, eliminating the need for a separate coil wire, e.g. GM High energy ignition system and some Toyota and Honda.
Many modern car engines have multiple ignition coils (one for each pair of cylinders) built into a coil pack, eliminating the need for a distributor and coil wire. Some car engines use a small ignition coil mounted on top of each spark plug, eliminating the need for spark plug wires entirely.
The average life span of a candle cable is about 50000 km (in the case of a mixed path). The wear of the spark plug wire leads first to an increase in fuel consumption and a loss in performance. The increased risk of a worn spark plug wire is the possibility of damaging the system downstream of the carburation.
abaut:
patig manufactures ignition wire set (spark plug cable set) for automobiles. Located in Iran, we have been researching and developing ignition cables since 2008. We are making ignition cable set for almost all of IRANKHODRO and SAIPA cars. Including general ignition cable set for 20 auto types, ignition wire set .
products :
Our products may appear to be like any other ignition cable set manufacturer’s products. However, there are all kinds of quality levels in the WIRE, BOOT’S, CAP, and CONNECTOR materials. Based on our extensive experience, we select and use only the best quality materials in our products for best performance. We never replace our products with low quality ones. We know our products represent every one of us working at patig. The overall quality of our products is so consistent that you do not have to evaluate samples after receiving our products.
quality:
- WIRE | |||||||||||||||||||||
1.silicon(outer cover)+silicon(inside cover) | |||||||||||||||||||||
- BOOT'S & CAP | |||||||||||||||||||||
1. silicon Cable Diameter: 7.0mm+/- 0.3mm
|
ISO 6856 test report | |
|
test |
< 80 N |
Insertion force |
20-70 N |
Removal force |
80 N |
Separation force |
1h under 35kV |
Dielectric breakdown |
48 hours |
Salt spray |
20 times -30&+200 C |
Thermal shock |
168 hours 180C |
Heat resistance |
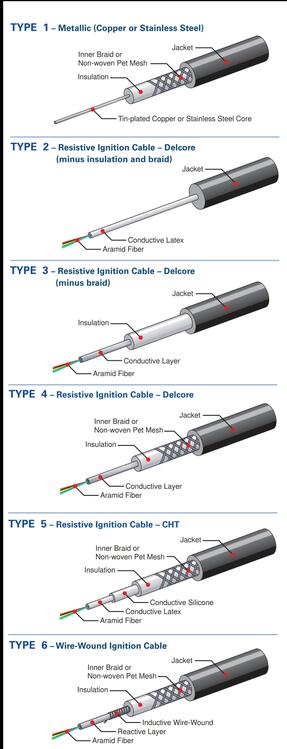
Instruction